Sliding Gate Valves

Sliding Gate Valves
Design principle of sliding gate valves
The sliding gate valves are characterised by a special throttle device in the functional unit that merely comprises two slotted disks that slide over each other and seal against each other. One sealing disc that is fitted in the housing perpendicular to the direction of flow has a predefined number of transverse slots. The second disc that is torque-proof and has the same arrangement of slots is moved perpendicular to the other one, this thereby changing the flow cross-section. The applied pressure differential presses the movable disc against the stationary disc.
The alternative when the demands are high
The sliding gate valve series controls liquid, vapour and gaseous media precisely, quickly and economically. A sealing disc (2) fixed in the body (1) at right angles to the flow direction has a certain number of crossways slots (3) . A moving disc (4) with the same arrangement of slots moves parallely to the fixed disc, thereby changing the flow cross section. The prevailing differential pressure presses the moving disc (4) against the fixed disc (2) and seals it.
Applications
Sliding gate valves are used to control and shut off gases, vapours and liquids
- Chemical and pharmaceutical industry
- Steel and aluminium plants
- Food and beverage industry
- Breweries
- Textile manufacturing
- Tyre production
- Plastics and rubber production
- Test bench technology
- Gas and compressed air production and utilisation
- etc.
The advantages of sliding gate valves
Compact design
Short installation length and extremely small actuators minimize the required space.
Easy to install and maintain
Thanks to the compact construction, the low weight (e.g. DN 150 with actuation a mere of approximately 15 kg) and the clever disc design reduces the installation and maintenance effort to a minimum.
Low leakage rate
< 0.0001% of the KVS value due to the self-lapping action of the moving disc and the pressure of the medium against the moving disc, using a surface seal instead of an annular seal.
Outstanding rangeability
from 30 : 1 to 160 : 1
Variable flow coefficient (KVS) valuesand characteristic curves
By simply replacing the fixed sealing disc, it is possible to change the flow coefficient (KVS) value and the characteristic curve at any time – from KVS 0.018 to 910.
Minimal wear
Related to the effect of the force which is applied at 90° to the direction of flow and minimised by the highly effective pairing of the materials used for the moving and fixed discs.
Maximum differential pressures
Control and shut-off of high differential pressures (up to 160 bar) with the smallest possible dimensions, compact length and low air consumption.
Variable flow coefficient (KVS) values and characteristic curves
– By simply replacing the fixed sealing disc:
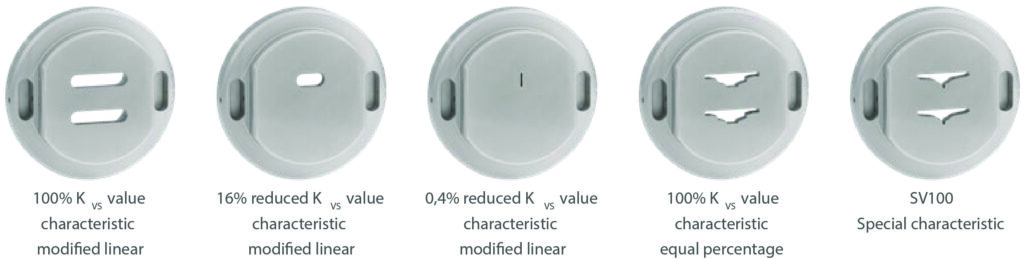
Optimal flow control
Avoids cavitation problems in the valve and operates quietly by lowering turbulence.
Saves resources and climate-friendly
Sliding gate valves are more compact and weigh much less than standard seat valves. This results in conscious use being made of valuable resources and CO2 being put to economical use in the production and during transportation. When in use, the GS valves benefit from a driving force that is reduced 10-fold. This reduces the energy consumption and is good for the climate and the environment.
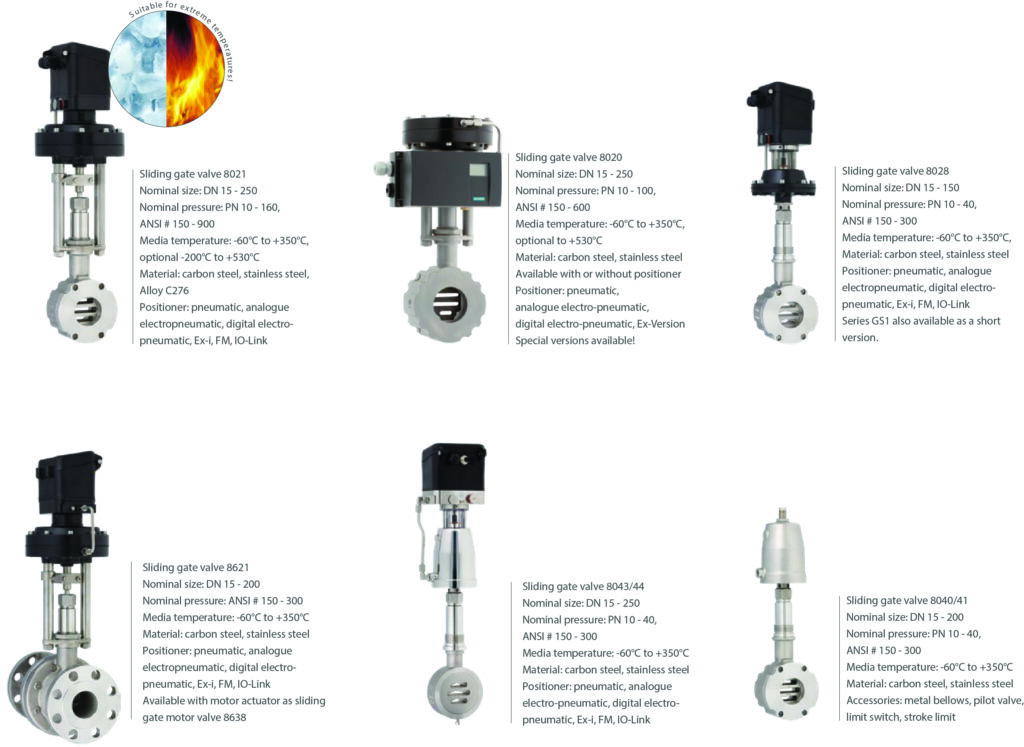
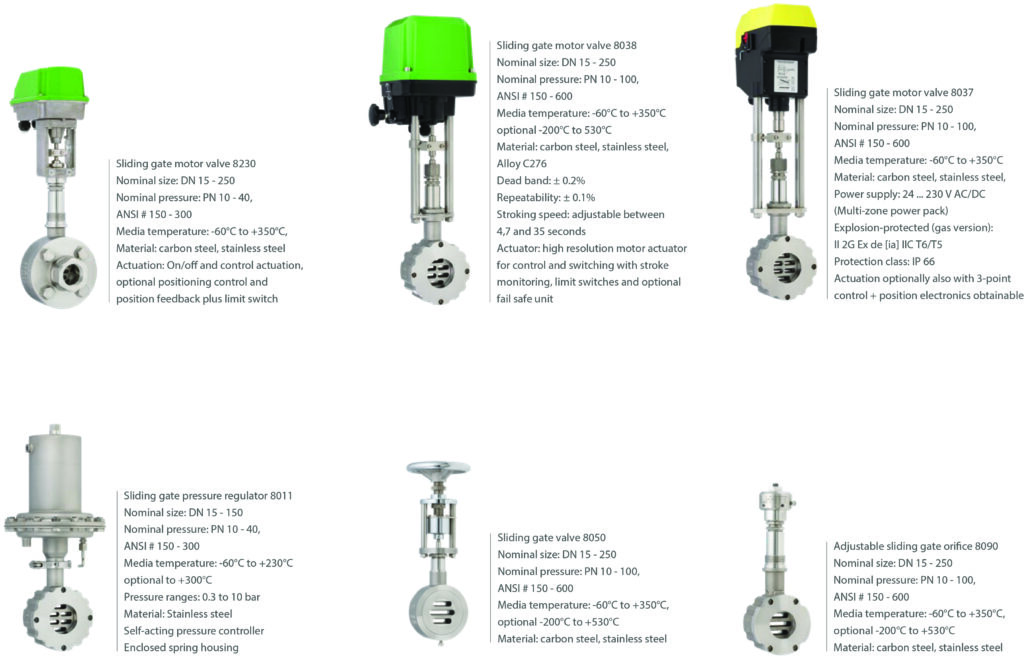